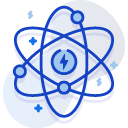
Manufacturing ERP System
A Manufacturing ERP (Enterprise Resource Planning) system is designed to integrate and streamline various manufacturing processes within an organization. It helps manage and optimize production, inventory, procurement, quality control, and other critical aspects of manufacturing operations. By providing real-time visibility and data-driven insights, a Manufacturing ERP system improves efficiency, reduces costs, and supports strategic decision-making.
Here’s an overview of the key components and features of a Manufacturing ERP system:
Key Components and Features
Production Planning and Scheduling:
Master Production Scheduling (MPS): Plan and schedule production activities based on demand forecasts and inventory levels.
Work Orders Management: Generate and track work orders for manufacturing processes.
Capacity Planning: Assess and manage production capacity to meet demand and avoid bottlenecks.
Inventory Management:
Real-Time Inventory Tracking: Monitor raw materials, work-in-progress, and finished goods in real time.
Automated Reordering: Set up automatic reordering of inventory based on predefined thresholds and demand patterns.
Warehouse Management: Optimize warehouse operations, including storage, picking, packing, and shipping.
Procurement and Supplier Management:
Supplier Management: Track supplier performance, manage relationships, and evaluate supplier reliability.
Purchase Orders: Create and manage purchase orders for raw materials and components.
Vendor Integration: Integrate with suppliers for electronic order processing and invoicing.
Quality Control and Assurance:
Quality Management: Implement quality control processes and standards to ensure product quality.
Inspection and Testing: Schedule and track inspections and testing of raw materials and finished products.
Non-Conformance Management: Record and manage non-conformance issues, including corrective and preventive actions.
Product Lifecycle Management (PLM):
Product Data Management: Manage product specifications, designs, and documentation throughout the product lifecycle.
Change Management: Track and manage changes to product designs and processes.
Configuration Management: Handle product configurations and variations effectively.
Costing and Financial Management:
Cost Tracking: Monitor and track production costs, including labor, materials, and overheads.
Cost Analysis: Analyze cost data to identify areas for cost reduction and efficiency improvements.
Financial Integration: Integrate with financial systems for seamless accounting and financial reporting.
Maintenance Management:
Preventive Maintenance: Schedule and manage routine maintenance tasks to prevent equipment breakdowns.
Work Order Management: Track maintenance work orders, including task details, scheduling, and completion status.
Asset Management: Manage and monitor equipment and machinery throughout their lifecycle.
Supply Chain Management:
Demand Forecasting: Use historical data and market trends to forecast demand and plan production accordingly.
Supplier Coordination: Work with suppliers to guarantee that components and materials are delivered on schedule.
Logistics Management: To guarantee prompt and economical delivery, streamline the distribution and logistics procedures.
Reporting and Analytics:
Real-Time Dashboards: Provide visual dashboards with real-time insights into key performance indicators (KPIs) and operational metrics.
Custom Reports: Generate customized reports for various aspects of manufacturing, such as production efficiency, inventory levels, and financial performance.
Data Analytics: Utilize data analytics to identify trends, predict issues, and make informed decisions.
10. Implementation Considerations:
Customization: Tailor the system to meet specific business needs and processes.
User Training: Provide training to ensure users are comfortable and proficient with the system.
Data Migration: Plan and execute the migration of data from legacy systems to the new ERP system.
Ongoing Support: Offer technical support and system maintenance to address any issues and updates.